В Волгоградской области начинается «Неделя без турникетов» – акция, в рамках которой школьникам и студентам ссузов показывают местные производства. Сейчас они модернизируются: внедряют всё больше автоматики, повышают объёмы производства. На одном из таких предприятий – Волгоградском керамическом заводе – 11 апреля побывали студенты и журналисты.
18 мая 2018 года на Волгоградском керамическом заводе (ВКЗ) в Красноармейском районе открыли новую линию по производству керамогранита. Общая стоимость строительства новой линии составила 1,2 млрд рублей, а построили её менее чем за год. Двумя годами ранее ВКЗ получил от федерального Фонда развития промышленности займ по лизинговой программе, который составил 100 млн рублей под 1% годовых сроком на 5 лет. Помимо этого, ВКЗ освободили от уплаты налога на добавленную стоимость (НДС) при покупке оборудования из Италии: аналоги в России не производятся. Сумма льгот составила около 50 млн рублей.
11 апреля на предприятии состоялся “День без турникетов”, на котором студентам Волгоградского колледжа им. Вернадского показали новую линию. Непосредственно данная акция проходит уже четвёртый год. Учащиеся школ и среднеспециальных учебных заведений знакомятся с работой промышленных предприятий Волгоградской области.
На предприятие приехал и замгубернатора Волгоградской области – председатель комитета промышленности и торговли Роман Беков. Вместе с гендиректором АО “Волгоградский керамический завод” Михаилом Шульженко они осмотрели новую линию по производству керамогранита.
– Российские военные в 1970-м году изобрели металл, который при температуре 1000 градусов сохранял механическую прочность, – рассказывает Михаил Шульженко во время демонстрации линии. – И тогда первая такая линия появилась в Волгограде, я её монтировал. Но у России она, к сожалению, не осталась. Итальянцы увидели её и пустили у себя такие конвейеры. А потом переделали под керамогранит. То есть мы изобрели, а они воспользовались.
Отдельное закрытое помещение на ленте – это “принтер”, использующий 8 разных красок. Он подбирает цвет и делает любой запрограммированный рисунок. “Можно хоть наш совместный снимок сделать и напечатать” – отметил Роман Беков. Журналисты поинтересовались, насколько данный рисунок устойчив к стиранию. Михаил Шульженко сообщил, что вообще такой рисунок вечный:
– Единственное, что некоторые виды мы не рекомендуем размещать на входах, где на первом этаже песок. Он является абразивом. Но это отдельные виды. А так – в торговых центрах, на фасадах, – её можно применять везде.
Далее продемонстрировали упаковочную линию, также полностью автоматизированную. 5-тонный робот самостоятельно осуществляет сортировку уже готовой продукции, а с другими машинами общается через Wi-Fi. Журналистов предупредили, что заходить за жёлтую линию нельзя. Впрочем, робот видит то, что происходит вокруг него, и если заметит рядом человека, то просто остановится и будет ждать, пока он не уйдёт. Рядом стоит отдельный бокс для зарядки аккумуляторов. Когда робот понимает, что энергии осталось мало, он сам подъезжает к нужной точке, ставит уже заряженный себе, а другой уходит на зарядку.
Михаил Шульженко обратил внимание, что раньше упаковкой занимались три человека. Пришла плитка, её отсортировали, упаковали в деревянные ящики, – и эти 20 кг на поддон. За одну смену выходило до 8 тонн погрузки. И вообще на одной линии работало 40 человек за смену. Сейчас же на всей линии керамогранита работает несколько человек, задача которых – следить за показателями автоматики. Роботы всё сортируют и грузят сами. О таких самоуправляющихся машинах гендиректор отзывается очень тепло:
– Им не нравится, когда они не работают, – улыбнулся Шульженко. – Их надо обслуживать вовремя, как и любую иностранную технику.
Гендиректор отметил, что можно вообще отказаться от человеческого труда на линии. “Но это будет завтра” – сказал Шульженко. Вообще же производительность труда выросла в 5-7 раз, а прежние работники ушли на другие участки. Однако на этом предприятие не планирует останавливаться:
– Мы предполагаем приобрести ещё один такой же комплекс для увеличения производства керамогранита. Это востребованная продукция, она высокого качества и имеет перспективу. До этого года экспорт осуществлялся только в пределах России и немного – на Кавказ и в Среднюю Азию. Сейчас есть договоры, по которым предполагаются первые отгрузки в Германию и Финляндию.
Всего ВКЗ выпускает более 100 наименований коллекций. Дизайн для керамики делает итальянская фирма, услугами которой пользуется весь мир. Сырьё получают с Урала, из Оренбурга, из Липецка, а большую часть – с Украины. Волгоградского сырья практически нет: “Местной глине надо отлежаться ещё где-то две тысячи лет” – улыбнулся Шульженко. Однако из регионального сырья используется только чапурниковский песок.
Роман Беков поделился своим мнением касаемо обновления ВКЗ:
– Данное предприятие является одним из высокотехнологических. Линия создана в 2018 году благодаря совместным действиям администрации региона, менеджмента предприятия и Министерства промышленности и торговли РФ. Проект реализован, в этом году он выходит на максимальные мощности, и продукты, которые выпускает в данный момент ВКЗ, востребованы как внутри России, так и за её пределами: более 15 стран мира являются её получателями.
Замгубернатора озвучил и планы по реализации на других площадках на этот год:
– На территории “Химпрома” будет создано новое предприятие, которое будет выпускать продукцию, очень важную для наших металлургов. Помимо этого, на той же площадке будут реализованы ещё два инвестпроекта общим объёмом финансирования около 1 млрд рублей. Это производство твёрдого натрия, и будет создано предприятие по производству пластикатов. В Михайловке будет завершён процесс по реконструкции печей Себряковцемента. Объём финансирования порядка 6 млрд рублей. В Волжском установят новое оборудование по выпуску карбоната. Также там будет создано новое предприятие по производству одноразовых контейнеров для забора крови.
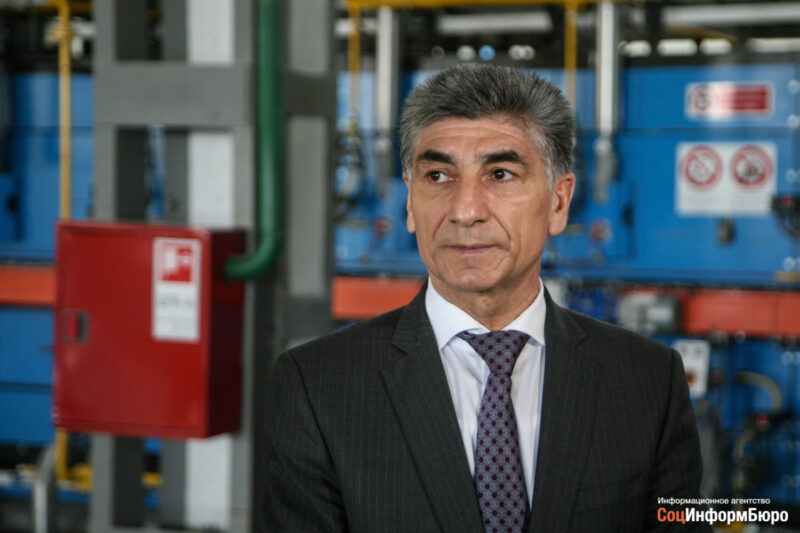
Отдельно Беков остановился на кадровом вопросе:
– Мы все прекрасно понимаем: то оборудование, которое видим здесь, студенты могут увидеть только на заводе, а не в тех заведениях, где они учатся. С этой целью мы проводим такие акции, как “Неделя без турникетов”, объясняем, рассказываем, чтобы максимально сблизить образовательные учреждения и заводы. Важно, чтобы наши учебные заведения понимали, какие нужны кадры для того оборудования, которое сейчас есть. Многие промышленные предприятия уже заключают соглашения с опорными вузами и техникумами. Мы максимально сближаем их, чтобы они были готовы к работе на наших промышленных предприятиях.
Параллельно посещению цеха керамогранита с замгубернатора студентам вначале провели экскурсию по плиточному цеху, после чего Михаил Васильевич уже “под своим крылом” повёл молодых ребят на линию керамогранита. Скучающих взоров практически не было: студентов впечатлило увиденное. Немало из них снимали линии и производство на свои телефоны. Один из студентов, Илья, который сейчас специализируется на автоматизации процессов, рассказал, что его впечатлил процесс цифрования плитки и работа печей. Поделился он и своими планами на будущее, сказав, что хотел бы работать на такой линии:
– Все сейчас внедряют инновации и автоматизацию. Добавляются новые технологии. Это будет всегда и везде, не только в России. За этим будущее. Конкуренции со стороны роботов не боюсь, – улыбнулся он.
Вместе со студентами на экскурсии был главный инженер Андрей Удовиченко, который также поделился своим видением нового производства:
– На предприятии я работаю 26-й год. Если говорить о старом производстве, то и производительность была другая, и объёмы производства, оборудование было хуже. Если брать цех, где мы сейчас находимся, он самый современный у нас на заводе. Если даже сравнивать с “классическим” производством, которое тоже является современным, то в данном случае собраны все передовые технологии, как зарубежные, так и наши. На самих работниках это отражается во всех сферах. Количество персонала сократилось, квалификация в разы возросла, особенно если брать тот цех, где мы находимся. Здесь без специалистов уже никак. Труд механизирован, автоматизирован, потому что даже если брать самую большую плитку массой 18 кг, то, сами понимаете, человек её физически просто не поднимет. Всё это делают машины. Без современных технологий выпускать высококачественную продукцию уже практически невозможно. Это признано во всём мире. Всех вновь принятых работников, а также наши специалисты обучаются, повышают квалификацию. Потому что, чтобы хорошего наладчика пресса подготовить, нужно минимум 2-3 года. Электронщика – та же самая ситуация. Есть люди одарённые, но в основной массе всё равно приходится довольно долго учить. Здесь деваться некуда: чтобы выпускать продукцию, соответствующую мировым стандартам, надо иметь и персонал, соответствующий им.
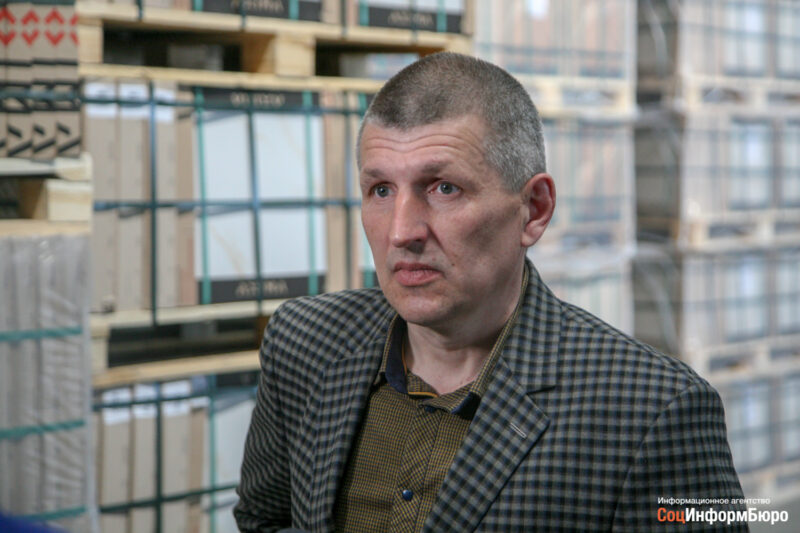